WELDING
The Significance of Welding in Railways
Welding is a critical process in the construction and maintenance of railway tracks, bridges, and various components. It involves joining metal pieces by melting their edges and fusing them together, creating a seamless and durable connection. In the context of railways, welding serves several essential functions:
The railway industry, with its extensive networks and heavy-duty demands, relies on precision engineering and robust construction. One fundamental aspect that underpins the safety and integrity of rail systems is welding. In this article, we delve into the crucial role that welding plays in railways, ensuring the strength and durability of tracks and infrastructure.
Welding is the invisible force that binds the railway industry together. It ensures the strength, durability, and safety of rail systems, tracks, and infrastructure. As technology advances and safety standards continue to evolve, welding remains a vital component in the ongoing success of rail transport, keeping trains on track and passengers and cargo moving safely across vast railway networks.

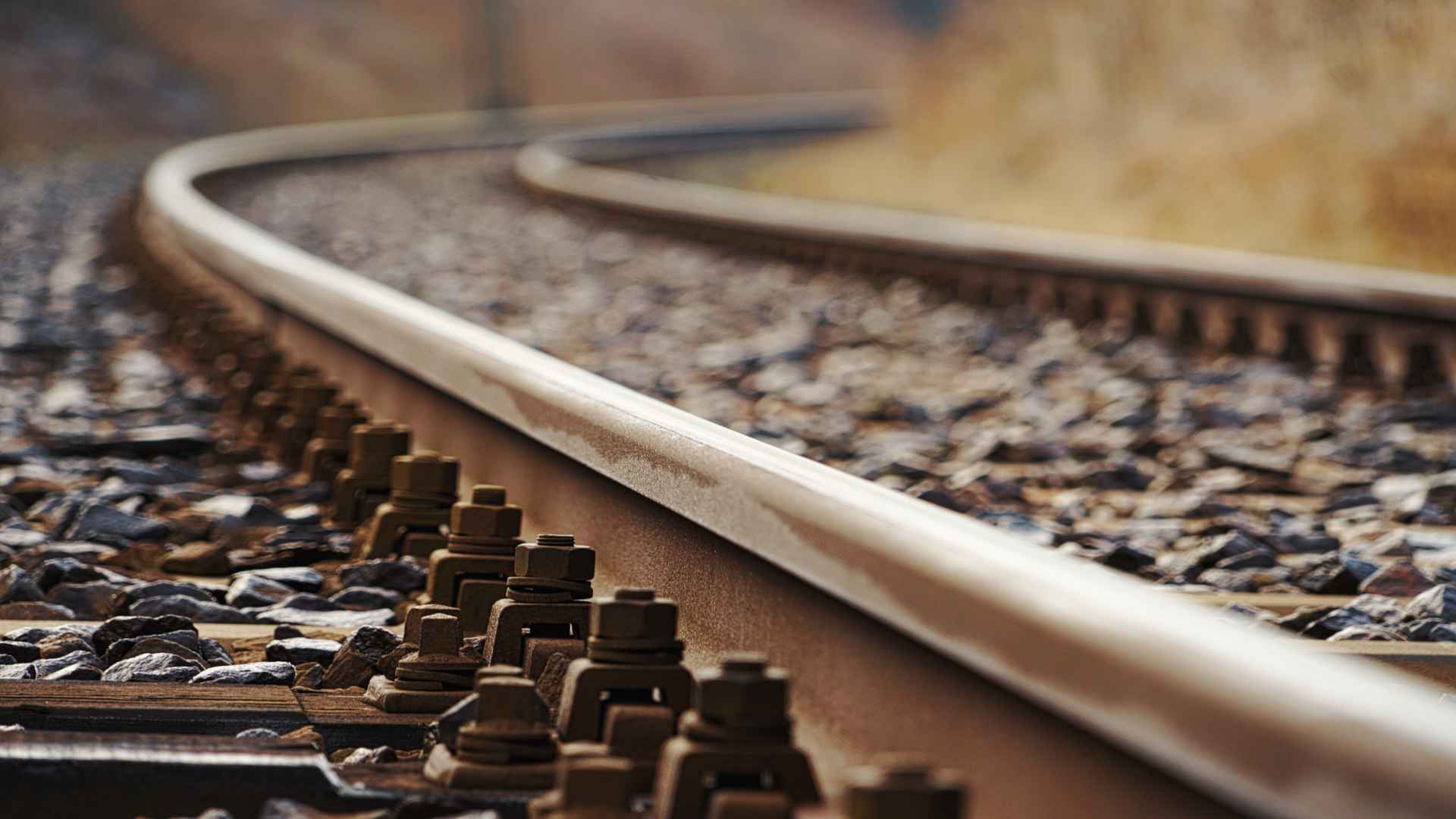
Rail Track Construction
Welding is extensively used to join rail sections, creating continuous tracks that are smooth, sturdy, and capable of withstanding the weight of trains and heavy cargo. Continuous welded rail (CWR) eliminates the need for rail joints, reducing maintenance and the risk of derailments.
Infrastructure Maintenance
Railway bridges, signal structures, and other infrastructure components often require welding for repairs and maintenance. Welding ensures that these structures remain safe and reliable for years to come.
Preventing Rail Wear
Rail wear is a natural consequence of continuous train traffic. Welding is used to build up worn rail profiles, extending the life of rails and minimizing the need for costly replacements.
Ensuring Track Alignment
Properly aligned tracks are essential for safe and efficient rail travel. Welding plays a role in securing the alignment of rail sections, reducing the risk of misalignment and accidents.

Several welding techniques are employed in the railway industry, including:
1. Flash Butt Welding: This method is commonly used to join rail sections. It involves applying an electric current to the rail ends, creating intense heat that melts the ends. The sections are then pressed together, forming a solid weld.
2. Thermit Welding: Thermit welding uses a chemical reaction to generate heat, which is used to melt the ends of rail sections. The molten metal fills a mold, creating a strong and durable weld.
3. Arc Welding: Arc welding techniques, such as shielded metal arc welding (SMAW), are used for various railway welding applications, including repairs and maintenance.
Quality assurance is paramount in railway welding. Welding must meet strict quality standards and undergo rigorous testing to ensure structural integrity and safety. Non-destructive testing (NDT) methods, such as ultrasonic testing and magnetic particle inspection, are commonly used to detect welding defects and ensure compliance with safety standards.

Accreditations & Acknowledge
ISA
